
Materials Processing
MATERIALS PROCESSING GROUP mainly focuses on materials development and processes. This includes ferrous and non-ferrous alloy development, solidification structures, thermo-mechanical processing, design of annealing cycle for industrial processes, hot dip coating development and its characterization, design of heat treatment cycles for various non-ferous materials and steels, metallic foams etc. are some of the research sub-areas of the group. The group houses a number of state-of-the-art materials processing facilities e.g. 0.5/1.0 T pneumatic forging hammers, 2/4 high hot and cold rolling mill, GleebleTM thermo-mechanical simulator, bench-type wire drawing m/c, air/vacuum heat treatment furnaces, jet erosion test system etc. A brief overview of the research endeavours/findings, in different research areas, follows.
Thermo-mechanical processing
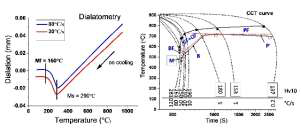
Thermo-mechanical processing holds one of the important keys for the evolution of microstructure and properties of ferrous alloy, non-ferrous alloys and steels. The group undertakes research on thermo-mechanical processing and heat treatment of specialty grade steels (e.g. line pipe steels, dual phase steels, high formable
automotive steels, bainitic steels, wear resistant steel, electrical steels and other alloys), thermodynamic and kinetics studies, particularly related to alloy development, and dynamic recrystallization behavior to satisfy the needs for high performance components and processes. Researchers are involved laboratory scale simulation/optimisation of plant process parameters for direct translation at industrial scale. The availability of state-of-the art GleebleTM 3800 thermo-mechanical simulator along with other processing and heat treatment facilities assist in the design and development of such materials.
Hot dip coating of steels
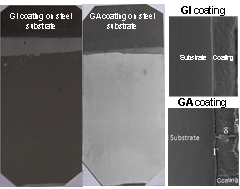
The research group is actively involved in developing high quality adherent hot dip coating on advanced high strength steels (AHSSs), particularly for automotive applications. Hot dip coatings on AHSS substrate impose several challenges due to the selective oxidation of various alloying elements present in the steel and complex microstructures of these types of steel. Therefore, the main focus of research activities pertaining to hot dip coating includes: (a) Alloy design for AHSSs suitable for developing quality coating (b) Design of annealing cycle to get the desired microstructure of substrate prior
to dipping (c) Optimization of bath composition and process parameters (d) Development of coating for high temperature applications.
Light metals and alloys
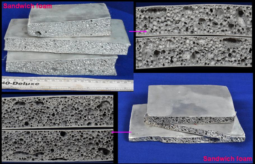
The group has a long experience in Al- and Mg-alloys and their composites, particularly employing in-house developed rheocasting facility. In addition, researchers are active in Strain Induce Melt Activation (SIMA) that transforms as-cast dendritic structure to fine globular shape grain morphology.
Sandwich Al foams have been developed using powder forging and rolling technique. The parameters for forging, rolling and sintering were optimized for different combinations of Aluminium (Al), Al-12Si and Al-8Si alloy. Foams were also developed incorporating SiC and flyash particles. The major achievement is the development of in-situ face-sheets on the foamed material. The pore sizes of the sandwiches varied between 2-4 mm and density of 0.4-0.7 g/cc could be achieved.